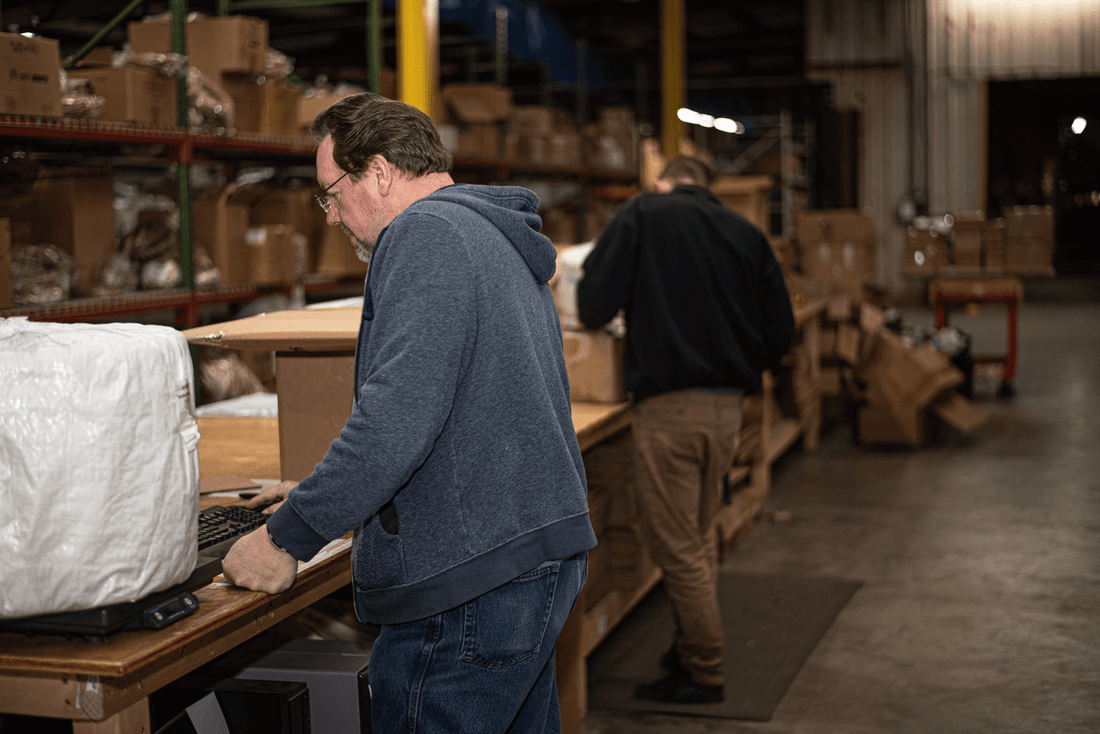
How to Calculate Warehouse Cost for Your Business?
Share
Product-based business owners know that the warehouse is an important aspect of the company. Whether you sell sneakers, electronics, or gluten-free snacks, you need a place to store, manage, and ship the products safely. Warehouse rental costs can be a huge expense for businesses, so it's important to calculate warehouse costs accurately and find ways to keep those costs down. Keeping a business running smoothly and generating revenue is directly correlated to understanding all warehouse costs.
Key Factors When Calculating Warehouse Costs
Many factors go into warehouse costs, so they must be clearly defined and easily understood. Learn how to calculate the cost of utilizing a warehouse to make the right decision for your company, eliminate any guesswork, and increase the bottom line.
Step One: Calculate Storage Space
Calculate the amount of storage space required for your inventory. Knowing the size of your products is a great starting point. From there, you can calculate warehouse rental costs based on the size of the products and how many you need on hand to fulfill orders. Keeping previous sales records and utilizing sales projections helps determine how many items you need.
Step Two: Calculate the Cost Per Square Foot
Once you know how much space is required to store your products, calculate the cost per square foot in rent, utilities, and other warehouse rental costs. If these calculations are for a new business, check local electricity rates to ensure your estimate is as close to an actual bill as possible. If calculating for an existing business, refer to previous electricity bills to calculate warehouse costs. If you have not yet bought or rented warehouse space, view comparable structure prices per square foot online. This will enable you to calculate warehouse rental costs accurately. Add up these numbers and other expenses to determine the total cost of warehouse space for your business.
Step Three: Pallets and Shipping Containers Count
Determine how many pallets and shipping containers you need to store the correct amount of inventory. Then, based on sales, calculate how many shipping containers you need to transport goods from one location to another.
Step Four: Shelving and Storage Needs
Each product-based business is different, and so are its warehouse needs. A warehouse for books will look a lot different than a warehouse for heavy appliances or bulky items. Consider what type of shelving and storage is needed for your particular product, and estimate how much it will cost to stock shelves with products based on weight and dimensions.
Step Five: Inventory Management System
Determine which type of inventory management system is best for your business. Then, choose how to move your products into and around the warehouse. Often a forklift is a crucial piece of equipment for moving and handling products. Some warehouses may use conveyor belts or rollers along with packing supplies.
Step Six: Tally and Compare
Add up all costs associated with running a warehouse, including labor, electricity, internet access fees, insurance coverage rates, etc., so you have an accurate idea of what it takes to operate your warehouse successfully each month. Compare these costs against potential profits to ensure enough money comes in to cover these expenses and keep the doors to your business open.
Choosing the Right Warehouse Solution
No business is alike. Each has unique practices that make the warehouse rental cost vary. Whether a small, two-person team or a larger company with multiple locations, businesses worldwide rely on third-party logistics providers (3PL) for all of their warehousing, distribution, and transportation needs. A 3PL can help take the load off of any business and save them time and money in the process. Consult with a 3PL when calculating your warehouse cost to see how they might be able to take your business to the next level for less.